Leading Manufacturers of CNC Lathe Machining Parts in China
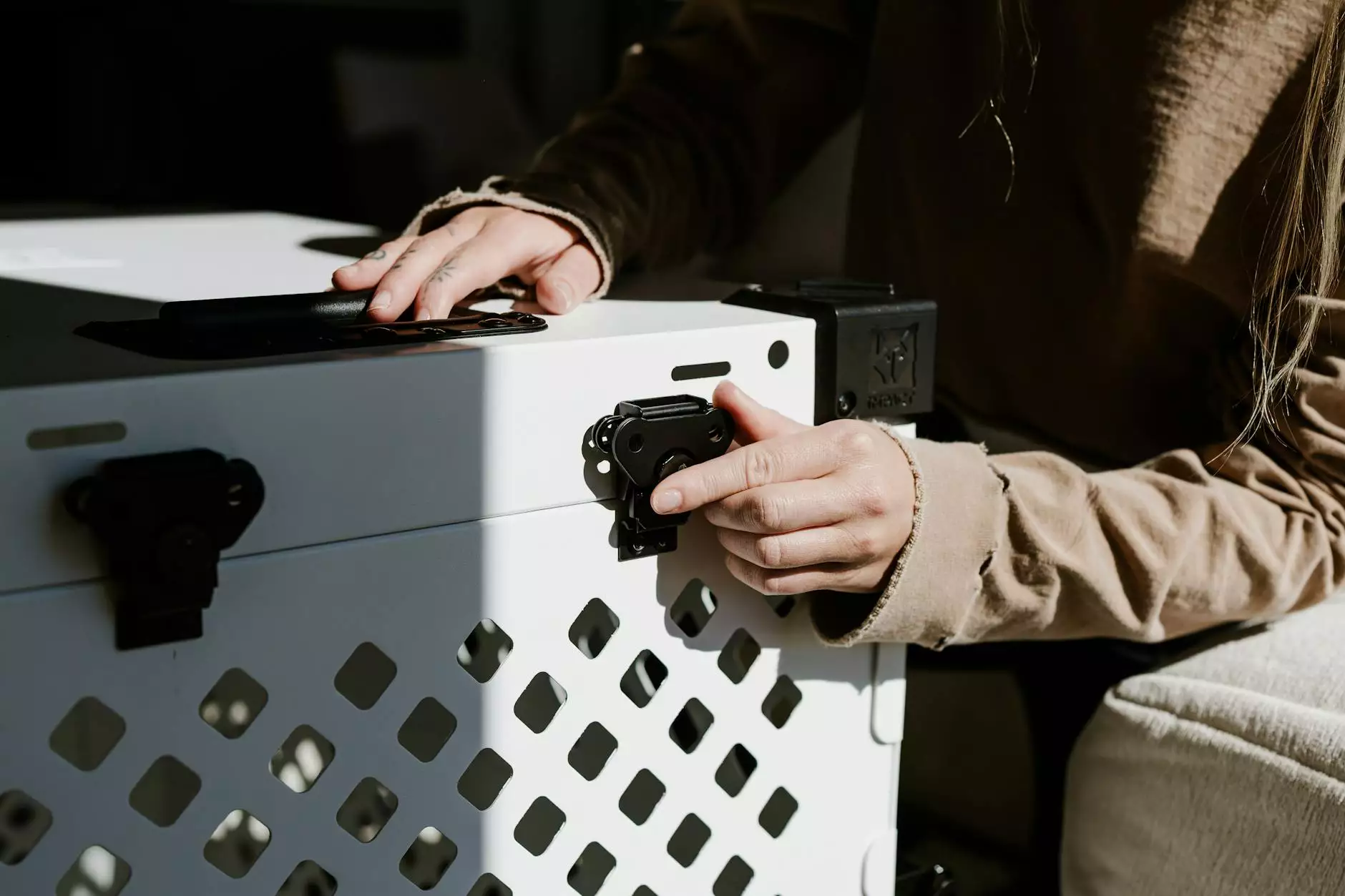
In today’s highly competitive industrial landscape, the demand for precision-engineered components is rising sharply. As businesses prioritize quality, efficiency, and cost-effectiveness, CNC lathe machining emerges as a pivotal process in metal fabrication. This article highlights the top China CNC lathe machining parts manufacturers, their technologies, and the significance of partnering with reliable suppliers like DeepMould.
Understanding CNC Lathe Machining
CNC lathe machining is a critical manufacturing process that utilizes computer numerical control (CNC) to automate the turning and machining of metal parts. This technique ensures high precision and repeatability, which are essential in producing complex geometries that meet stringent specifications.
- Precision: CNC lathes can produce components with tolerances as tight as ±0.001 inches.
- Efficiency: Once a program is written, CNC machines can produce parts continuously with minimal human intervention.
- Versatility: CNC lathes can handle a wide range of materials including steel, aluminum, and plastics.
- Automation: This process reduces human error and allows for lights-out manufacturing.
The Landscape of CNC Lathe Manufacturers in China
China has established itself as a global leader in manufacturing, particularly in the field of CNC machining. The emergence of advanced technologies paired with competitive pricing has positioned numerous Chinese manufacturers at the forefront of the industry. Here are some notable attributes that characterize the best China CNC lathe machining parts manufacturers:
1. Advanced Technological Integration
Leading manufacturers in China leverage state-of-the-art machinery and software to enhance their production capabilities. They invest heavily in the latest CNC technologies, such as:
- High-Speed Machining: Increases the production rate and reduces cycle times.
- Multifunctional Machines: Capable of performing multiple processes (turning, milling, grinding) within a single setup.
- Robotics and Automation: Implementing robotic arms for handling, assembly, and quality inspection to ensure efficiency.
2. Quality Assurance Systems
World-class manufacturers in China adopt rigorous quality control measures to ensure that every component meets international standards. This includes:
- ISO Certifications: Compliance with ISO 9001 standards signifies a commitment to quality management.
- In-House Inspection Labs: Utilizing precision instruments for dimensional checks, surface finish evaluations, and material composition analysis.
- Customer Feedback Loops: Actively incorporating client feedback to continuously improve products and services.
3. Customization Capabilities
One of the defining features of leading China CNC lathe machining parts manufacturers is their ability to provide tailored solutions. Their capabilities include:
- Custom Designs: Collaborating with clients to develop components that fit specific requirements.
- Material Selection: Offering a diverse range of materials to choose from, ensuring the right fit for every application.
- Prototyping Services: Allowing for rapid prototyping to validate designs before full-scale production.
Spotlight on DeepMould
DeepMould is a leader in the field of metal fabrication and CNC machining. With a dedication to excellence and customer satisfaction, DeepMould stands out among China CNC lathe machining parts manufacturers for several reasons:
1. Comprehensive Service Offering
DeepMould provides a wide range of services beyond CNC turning, including:
- CNC Machining: Covering milling, grinding, and electrical discharge machining (EDM).
- Injection Molding: Complementing CNC services with injection molding capabilities for plastic components.
- Assembly Services: Offering full assembly solutions ensures a complete product delivery to clients.
2. Strong Customer Focus
DeepMould believes that successful partnerships stem from understanding customer needs. Their approach includes:
- Collaborative Design Process: Working closely with clients at every stage from conception to production.
- Flexible Production: Adapting to changing client requirements without compromising efficiency.
- Timely Delivery: Commitment to meeting deadlines to keep clients on schedule.
3. Focus on Sustainability
In an era of increasing environmental awareness, DeepMould is committed to sustainable manufacturing practices by:
- Minimizing Waste: Implementing optimized machining processes to reduce scrap rates.
- Energy Efficiency: Utilizing energy-efficient machinery to decrease overall energy consumption.
- Responsible Sourcing: Ensuring that all materials meet environmental regulations and are sourced ethically.
Challenges and Solutions in CNC Machining
Despite its advantages, the CNC machining industry faces various challenges, including:
1. Supply Chain Disruptions
The global nature of manufacturing can lead to unforeseen supply chain interruptions. Solutions include:
- Diverse Sourcing: Establishing relationships with multiple suppliers to mitigate risks.
- Inventory Management: Keeping an optimized stock of critical materials to buffer against shortages.
2. Skilled Labor Shortages
The demand for skilled labor in CNC machining exceeds supply. Manufacturers can address this by:
- Training Programs: Implementing in-house training to develop employee skills.
- Apprenticeships: Partnering with educational institutions to foster new talent in the industry.
3. Technological Adaptation
As technology evolves, manufacturers must adapt continually. Strategies to stay ahead include:
- Continuous Learning: Investing in workforce development to keep employees updated with the latest technologies.
- Research and Development: Fostering a culture of innovation to embrace new manufacturing technologies as they arise.
The Future of CNC Lathe Machining in China
The future of CNC lathe machining in China appears promising. As Chinese manufacturers innovate and expand their capabilities, they are poised to retain leadership in the global market. The integration of technologies such as:
- Artificial Intelligence: To enhance automation and process optimization.
- Industry 4.0: Implementing smart manufacturing techniques to revolutionize production efficiency.
- 3D Printing: Complementing traditional machining for complex prototypes and low-volume production.
Conclusion
As the demand for precision and quality rises, choosing the right China CNC lathe machining parts manufacturers is more crucial than ever. With leaders like DeepMould at the forefront, businesses can rely on innovative solutions, superior craftsmanship, and a commitment to excellence. By partnering with trusted manufacturers, companies can ensure they stay competitive and continuously meet market demands.
Investing in quality CNC machining parts not only contributes to the production of superior end products but also promotes sustainability and innovation within the industry. The future is bright for businesses that embrace precision manufacturing, and with the continued evolution of technology, the possibilities are virtually limitless.