The Vital Role of Plastic Injection Molding Manufacturers in Modern Industries
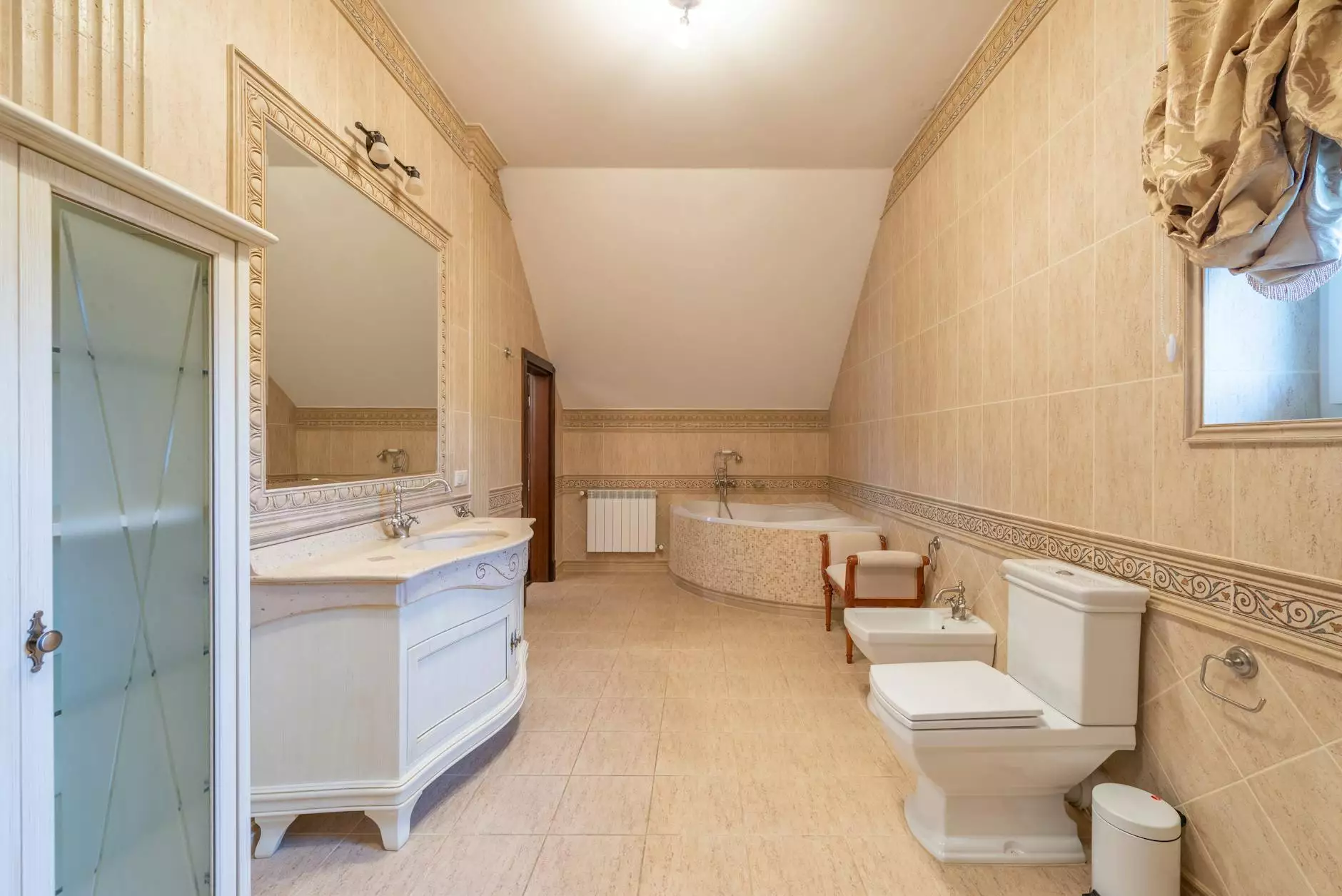
Plastic injection molding manufacturers play an indispensable role in various sectors, most notably in the manufacturing of components for the electronics and medical supplies industries. This article delves deep into the processes, advantages, and future of plastic injection molding and its importance in manufacturing.
What is Plastic Injection Molding?
Plastic injection molding is a highly efficient manufacturing process used to create parts by injecting molten plastic into a mold. This process is favored for its ability to produce large volumes of parts with high precision and minimal waste.
How Does the Process Work?
- Material Preparation: The process begins with the selection of plastic pellets that are fed into the injection molding machine.
- Melting: The pellets are heated until they melt into a viscous liquid.
- Injection: The molten plastic is then injected under high pressure into a mold.
- Cooling: Once the mold is filled, the plastic is cooled to solidify it into the desired shape.
- Demolding: The mold is opened, and the finished part is ejected.
The Importance of Precision in Plastic Injection Molding
Precision is paramount in industries like electronics and medical supplies. Components must meet exact specifications to ensure functionality and safety. Plastic injection molding manufacturers utilize advanced technologies like CAD (Computer-Aided Design) and CAM (Computer-Aided Manufacturing) to design molds with meticulous detail.
Applications of Plastic Injection Molding in Electronics
The electronics industry is one of the largest consumers of injection-molded plastic parts. Here’s a closer look at how this manufacturing process impacts this sector:
Key Components Manufactured
- Consumer Electronics: Cases and enclosures for smartphones, tablets, and other devices.
- Connectors: Precision connectors for circuit boards.
- Switches: Components used in various electrical devices.
The Benefits of Injection Molding for Electronics
Using injection molding in the electronics manufacturing process offers several benefits, including:
- High Volume Production: Capable of producing thousands of identical parts quickly.
- Cost Efficiency: Reduces waste and lowers production costs.
- Complex Geometries: Allows for intricate designs that are often lightweight yet durable.
Applications of Plastic Injection Molding in Medical Supplies
In the medical supplies field, plastic injection molding is crucial for developing reliable, clean, and precise components. Let’s explore its applications:
Key Components Manufactured
- Medical Devices: Components for devices such as syringes, inhalers, and diagnostic equipment.
- Packaging: Safe and sterile containers for pharmaceuticals and surgical instruments.
- Implants: Durable and biocompatible components used in surgeries.
The Advantages of Injection Molding in Medical Applications
The use of plastic injection molding in the medical field presents unique advantages:
- Regulatory Compliance: Manufacturers must adhere to strict regulations, ensuring safety and efficacy in medical environments.
- Cleanroom Manufacturing: Many medical parts are produced in sterile environments to prevent contamination.
- Customization: Ability to create tailored solutions for specialized medical needs.
Choosing the Right Plastic Injection Molding Manufacturer
When selecting a plastic injection molding manufacturer, several factors should be considered:
Factors to Consider
- Experience: Look for manufacturers with a proven track record in your industry.
- Technology: The latest technologies can enhance precision and efficiency.
- Quality Assurance: Ensure the manufacturer implements rigorous quality control measures.
- Customer Support: Strong communication and support are essential for seamless collaboration.
Establishing a Partnership
Building a strong partnership with a manufacturer involves clear communication, mutual trust, and transparency. A productive collaboration can lead to innovation and enhanced quality in your products.
The Future of Plastic Injection Molding
The world of plastic injection molding is continuously evolving, driven by technological advancements and changing industry demands. Here are some emerging trends:
Technological Advancements
- Automation: Increased use of robotics for faster and more accurate production.
- 3D Printing: Integrating additive manufacturing with injection molding processes for rapid prototyping.
- Sustainable Practices: Advances in bio-based plastics and recycling technologies to reduce environmental impact.
Challenges and Opportunities
As the industry adapts to new materials and practices, it also faces challenges such as:
- Material Costs: Fluctuating costs of raw materials can impact production budgets.
- Skill Gap: The demand for skilled workers in high-tech manufacturing is higher than the supply.
However, these challenges present opportunities for innovation and investment in workforce training and development.
Conclusion
In conclusion, the role of plastic injection molding manufacturers cannot be overstated. From the creation of crucial components in electronics to the manufacture of precise medical supplies, these manufacturers are fundamental to the success of multiple industries. As technology continues to evolve, the future looks promising, unlocking new potential for efficiency and sustainability in manufacturing. By understanding the nuances of this process, businesses can leverage the advantages of plastic injection molding to stay competitive and innovate in their respective fields.