The Premier Guide to Prototype Injection Molding
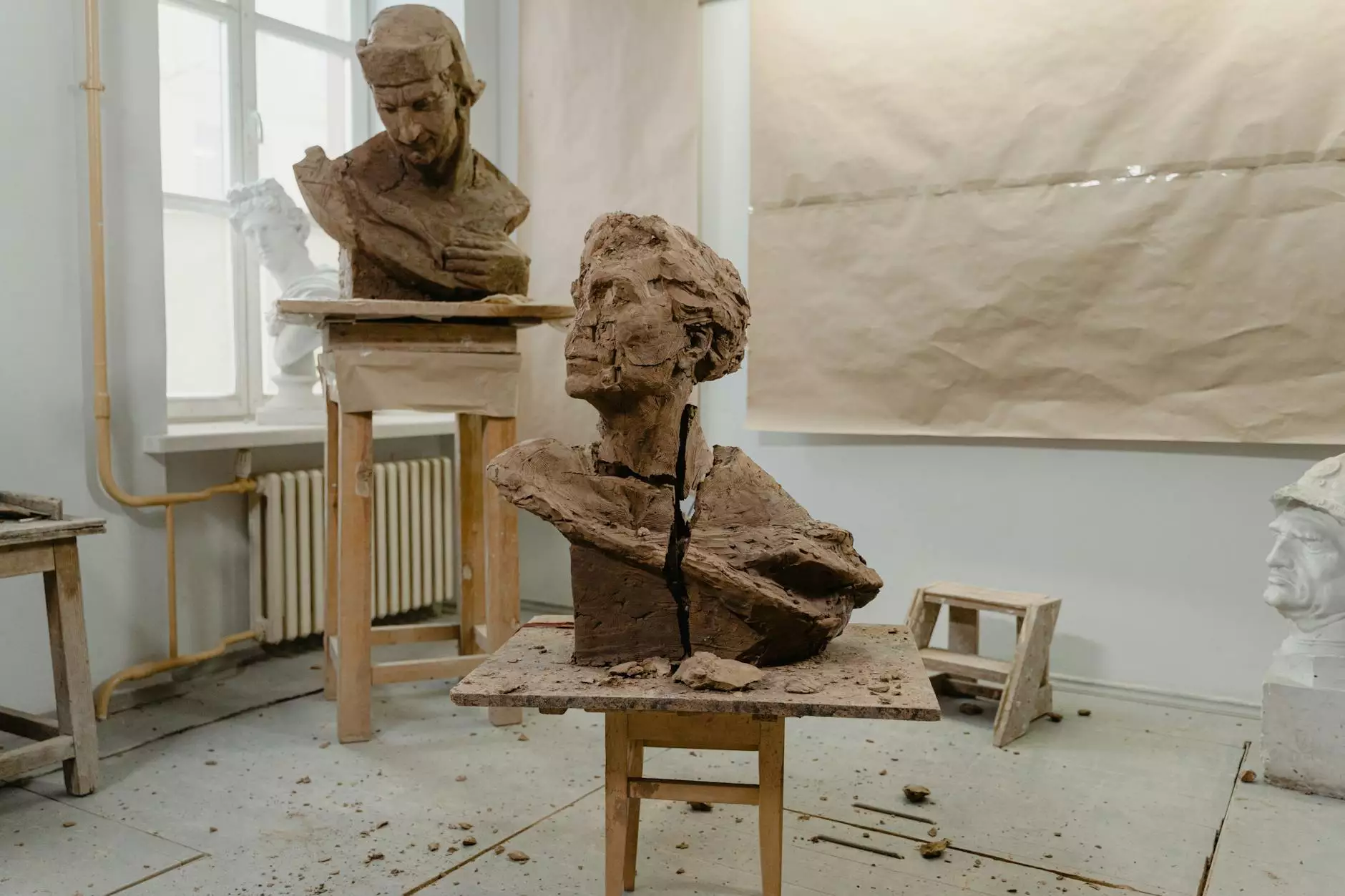
In the ever-evolving landscape of manufacturing, prototype injection molding stands as a beacon of innovation and efficiency. This advanced manufacturing process not only facilitates the rapid development of prototypes but also optimizes costs and ensures quality control in product development. Companies such as DeepMould.net are paving the way in this domain, particularly within the category of Metal Fabricators.
Understanding Prototype Injection Molding
Prototype injection molding is a technique used to create precise prototypes for various products quickly and cost-effectively. This process involves injecting molten material into a mold to form complex shapes and designs. The accuracy and repeatability of injection molding make it an ideal choice for businesses seeking to test and refine their products before mass production.
How Prototype Injection Molding Works
Step-by-Step Process
- Design Creation: Initially, a product design is developed, often utilizing sophisticated CAD (Computer-Aided Design) software to create a digital prototype.
- Mold Fabrication: After the design is finalized, a mold is crafted from robust materials, typically metals or high-grade plastics, to withstand the injection process.
- Material Selection: The choice of material is critical in achieving the desired properties of the prototype. Common materials include thermoplastics and thermosetting polymers.
- Injection Process: The molten material is injected into the mold under high pressure, allowing it to fill all the intricate details of the mold.
- Curing and Cooling: Once the material cools and solidifies, the mold is opened to retrieve the finished prototype.
- Post-Processing: Additional finishing, such as trimming or polishing, may be required to achieve the final product specifications.
Benefits of Prototype Injection Molding
Transitioning to prototype injection molding offers numerous benefits for businesses, particularly in the metal fabrication sector.
- Cost-Effective: With lower production costs and minimal material waste, this process is economically advantageous, especially for startups and small businesses.
- Time Efficiency: Rapid production timelines enable firms to iterate designs quickly, facilitating faster entry into the market.
- High Precision: The accuracy of injection molding ensures that each prototype mirrors the final product closely, reducing the likelihood of costly errors in later production stages.
- Material Versatility: A wide range of materials can be used, allowing businesses to choose according to the required strength, flexibility, and durability of their products.
- Scalability: Once a prototype is finalized, the same mold can be used for mass production, streamlining the transition from design to manufacturing.
Applications of Prototype Injection Molding
The versatility of prototype injection molding makes it suitable for a broad range of applications across various industries, including:
1. Consumer Products
In the consumer goods sector, where aesthetic and functional innovation is crucial, prototypes created through injection molding allow for extensive testing of form, fit, and function.
2. Automotive Industry
Automobile manufacturers use this method to develop intricate components that require high precision and reliability, ensuring safety and performance.
3. Medical Devices
In the healthcare industry, the strict regulations demand high-quality prototypes for devices. Injection molding meets these requirements by enabling consistent production of complex geometries.
4. Electronics
The fast-paced electronics sector often relies on prototype injection molding to keep up with technological advancements and consumer demands.
Choosing the Right Partner for Prototype Injection Molding
When selecting a partner for prototype injection molding, consider these key factors:
- Experience: Look for partners with a proven track record in manufacturing and prototyping, particularly in your industry.
- Technology: Ensure the partner utilizes the latest technology and equipment to produce high-quality prototypes efficiently.
- Material Capability: Check that they offer a wide array of materials, allowing you to explore different properties for your prototype.
- Customer Service: Excellent communication and support throughout the process can significantly enhance the collaboration experience.
- Cost Transparency: A reputable partner will provide detailed quotes and explanations regarding the costs involved.
The Role of DeepMould.net in Prototype Injection Molding
At DeepMould.net, we leverage years of expertise in the metal fabrication industry to offer advanced prototype injection molding solutions. Our commitment to quality, efficiency, and customer satisfaction ensures that your prototypes not only meet but exceed expectations.
Why Choose DeepMould.net?
- State-of-the-Art Facilities: Our manufacturing facilities are equipped with cutting-edge technology that guarantees precision and quality in every prototype.
- Expert Team: Our team of specialists brings extensive knowledge in design, engineering, and manufacturing, allowing us to solve complex challenges efficiently.
- Tailored Solutions: We understand that every project is unique, and we provide customized solutions that meet your specific needs and objectives.
- Rapid Turnaround: We value your time and strive to deliver prototypes swiftly, ensuring you can move forward in your project without delays.
- Comprehensive Support: From the initial consultation to the final delivery, our dedicated customer service team is with you every step of the way.
The Future of Prototype Injection Molding
The future of prototype injection molding looks promising as advancements in technology continue to evolve the capabilities of the process. Innovations such as:
- 3D Printing Integration: Combining 3D printing with injection molding can expedite the design phase and reduce costs.
- A.I. and Machine Learning: These technologies can optimize mold design, predict potential issues, and improve process efficiency.
- Advanced Materials: The development of new materials will expand the possibilities of what can be achieved through injection molding, including biodegradable and smart materials.
Conclusion
In conclusion, prototype injection molding is a fundamental part of modern manufacturing and product development. Its numerous advantages, coupled with the expertise provided by companies like DeepMould.net, make it an invaluable resource for businesses striving to innovate and excel in their respective industries. The ability to produce high-quality prototypes quickly and cost-effectively enhances the overall product development cycle, diminishing time to market and optimizing customer satisfaction.
As you embark on your journey of product development, consider the significant role that prototype injection molding will play in ensuring your success. Embrace the future of manufacturing with the right partners by your side, and watch your ideas turn into reality.