Unlocking Excellence in Metal Fabrication: The Critical Role of High Pressure Die Casting Products in Modern Manufacturing
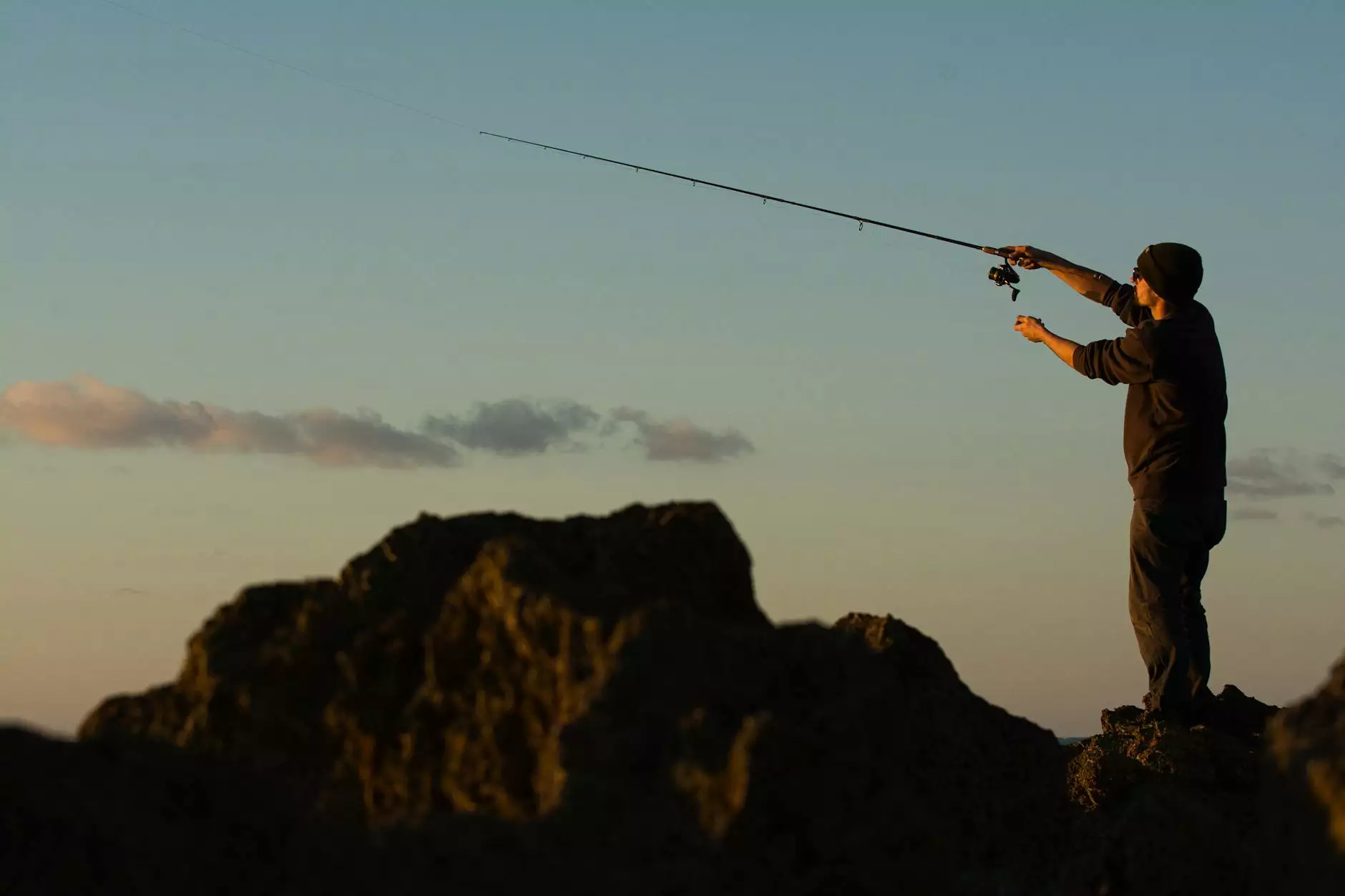
In today’s highly competitive industrial landscape, manufacturers and engineers are continually seeking advanced, reliable, and cost-effective methods to produce complex metal components. At the forefront of these techniques is high pressure die casting (HPDC)—a precision process that has revolutionized the way metals are shaped into high-quality, durable, and intricate parts. This article offers an extensive deep dive into the realm of high pressure die casting products, highlighting their significance within the domain of metal fabricators like DeepMould.net, and how they solidify their position as industry leaders.
Understanding High Pressure Die Casting: An Essential Manufacturing Technique
High pressure die casting is a manufacturing process that involves forcing molten metal under high pressure into a meticulously crafted die mold. This process generates precise, high-quality metal components with intricate designs and superior surface finishes. The method is particularly favored for producing large-volume, complex shapes, and parts requiring tight dimensional tolerances.
The Core Components of HPDC
- Die Mold: The reusable steel mold designed to shape the molten metal.
- Molten Metal: Usually alloys such as aluminum, zinc, magnesium, or copper.
- High-Pressure Injection System: Pumps the molten metal rapidly into the die cavity.
- Ejection System: Facilitates the removal of the finished component once solidified.
The Advantages of High Pressure Die Casting Products
Choosing high pressure die casting products offers a multitude of advantages that make this technique a preferred option among metal fabricators. Some of these benefits include:
Exceptional Precision and Complex Design Capabilities
HPDC allows for manufacturing highly intricate and detailed parts with tight tolerances—something that traditional casting methods cannot easily achieve. This ensures consistency and reliability in mass production.
Superior Surface Finish and Aesthetic Appeal
The smooth surface finish resulting from the high-pressure process reduces the need for additional machining or finishing, saving time and costs. This is particularly beneficial for consumer electronics, automotive parts, and decorative components.
Material Advantages and Weight Reduction
HPDC is compatible with lightweight metal alloys like aluminum and magnesium, contributing to weight reduction in applications such as automotive and aerospace industries, thereby enhancing fuel efficiency and performance.
Cost-Effectiveness and High Productivity
Once the tooling is established, high volume production becomes economical due to the speed of casting cycles and low labor costs—offering a high return on investment for businesses engaged in large-scale manufacturing.
Mechanical Strength and Durability
The densely packed metal structure resulting from HPDC imparts excellent mechanical properties, making the products suitable for demanding applications where strength and longevity are paramount.
Critical Factors in Producing High Pressure Die Casting Products
Producing top-quality high pressure die casting products necessitates meticulous attention to several crucial factors:
Choice of Alloy
The selection of alloy significantly influences the final product's strength, corrosion resistance, and machinability. Aluminum alloys, such as A356 or A380, are popular due to their excellent balance of weight and strength.
Precision in Die Design and Manufacturing
The die must be engineered with exacting precision, incorporating venting channels, cooling systems, and draft angles to ensure smooth casting and easy ejection of finished parts.
Control of Process Parameters
Factors like injection pressure, temperature, and speed need strict regulation to avoid defects such as porosity, cold shuts, or incomplete fillings.
Post-Casting Treatments
Finishing processes such as deburring, shot peening, coating, or anodizing enhance the corrosion resistance, appearance, and functional performance of the final products.
The Role of Expert Metal Fabricators in Shaping High Pressure Die Casting Products
Leading metal fabricators like DeepMould.net employ cutting-edge technology and skilled craftsmanship to produce high-pressure die castings that meet the most rigorous standards. Their expertise extends across the entire manufacturing spectrum, from:
- Initial design and prototyping with CAD/CAM tools
- Precision die manufacturing with CNC technology
- Optimizing casting parameters for defect minimization
- Implementing inspection and quality control measures
- Providing tailored finishing solutions
Innovative Trends Shaping the Future of High Pressure Die Casting Products
The industry continues to evolve, driven by technological innovations and increasing demands for smarter, lighter, and more environmentally friendly components. Key trends include:
Automation and Industry 4.0 Integration
Utilizing AI-driven monitoring systems and automated die casting machines increases production efficiency, accuracy, and traceability, ensuring consistent quality.
Sustainable and Eco-Friendly Practices
Recycling metal scrap, reducing energy consumption, and implementing green manufacturing protocols minimize environmental impact while maintaining product quality.
Advanced Alloy Development
Research into new high-performance alloys offers opportunities for lighter, stronger, and corrosion-resistant die-cast components, opening new frontiers in various industries.
Why Partner with DeepMould.net for Your High Pressure Die Casting Products
As a premier metal fabricator specializing in high pressure die casting, DeepMould.net boasts a reputation built on precision, innovation, and customer-centric solutions. Their advantages include:
- State-of-the-art die casting facilities with advanced automation
- Expert team with decades of experience in design, manufacturing, and quality control
- Comprehensive service from prototyping to mass production
- Strict adherence to international standards such as ISO 9001 and ISO/TS 16949
- Commitment to eco-friendly practices and sustainable manufacturing
Conclusion: Embracing the Future of Metal Fabrication with High Pressure Die Casting
In the dynamic landscape of metal manufacturing, high pressure die casting products stand out as a game-changing technique that offers unmatched precision, efficiency, and versatility. Whether serving the automotive, aerospace, electronics, or consumer goods industries, the quality and reliability of HPDC make it an indispensable part of modern metal fabricator capabilities.
To stay ahead in this competitive arena, partnering with industry leaders like DeepMould.net ensures access to cutting-edge technology, expert craftsmanship, and innovative solutions tailored to your specific needs. Investing in premium quality high pressure die casting products is not just about manufacturing parts; it's about building trust, reputation, and long-term success.
Contact Us Today to Discover Our Superior High Pressure Die Casting Products
Get in touch with DeepMould.net to discuss your project requirements and experience the highest standards in metal fabrication and high pressure die casting. Together, let's shape the future of manufacturing innovation.